How do you bridge the gap between a growing need for manufacturing hires and a shrinking number of qualified candidates — so you can stay ahead of competitors?
What you need to know:
- The US manufacturing sector faces a widening skills gap due to retiring baby boomers, lack of a robust talent pipeline, and the increasing demand for digital and technical skills driven by Industry 4.0 advancements like AI integration, better robotics, and IoT devices (The Manufacturing Institute).
- Despite a projected need for nearly 4 million new employees by 2033, half of those positions may remain unfilled as manufacturers struggle to attract younger, skilled workers and retain existing talent (Deloitte).
- Companies can bridge the skills gap by using pre-hire assessments to evaluate both hard and soft skills, enabling them to identify high-potential candidates and improve their hiring process.
The US manufacturing sector has been struggling with a skills gap for the last decade — and the gap is only growing wider. As tech advancements spur a need for digital skills in the sector, domestic production ramps up, and baby boomers exit the workforce, attracting a younger cohort — especially one that can fill high-skill jobs — has been the top challenge for most companies.
According to Deloitte and the Manufacturing Institute, between 2024 and 2033, the US manufacturing sector is expected to need nearly 4 million new employees due to growth, rehiring, and reshoring efforts. However, if the current challenges facing the workforce still persist, roughly half of those positions could stay vacant.
From 2017 until 2024, studies by NAM identified that manufacturing leaders put “attracting and retaining a quality workforce” as their top concern most of the time. Even in Q1 2025, manufacturers faced with trade uncertainties, increased cost of raw materials, and rising healthcare and insurance costs still put workforce concerns in fourth place among business challenges, above supply chain challenges and an unfavorable business climate.
Faced with a global shortage in high-skill talent for manufacturing positions, what can a single company do to protect their own hiring practices and their bottom line?
Why is there a growing skills gap?
The growth in the manufacturing sector, on its surface, should be good news for the industry. But years of declining interest in the sector, made up of a misperception of blue collar work and the absence of a sturdy talent pipeline, plus competition from other sectors, is pushing potential employees away.
Baby boomers exiting the workforce
Baby boomers are retiring — and Gen Z and millennial applicants need to fill the gap. The exit of highly-skilled workers has left a void, yet there are few candidates qualified enough to fill those roles. This is primarily due to another, adjacent issue — a lack of individuals pursuing traditional manufacturing education.
Decline in manufacturing education
A long-established preference for a college education has pushed many potential workers away from pursuing trade school or apprenticeships for manufacturing positions. While the number of bachelor degrees issued has increased, the number of associate degrees, which can prepare individuals for skilled trades, has leveled off. However, interest in certification training has actually ramped up — four times more than associate degrees for manufacturing-related programs.
Certification vs. certificates
Not all roles come with standardized certifications for their fields. While many training companies and educational institutions sell courses that include “certification,” only some are based on a widely applicable standard body of knowledge. Because individuals are prone to lie on their resumes and not all “certificates” can be verified, it’s important to balance hiring based on nontraditional certification with testing in your own hiring practices in order to determine that a candidate’s skills line up with what you need in an organization. Flexible pre-hire assessments can help you pick and choose the candidates that best fit the role you’re hiring for.
Changing skill requirements
A study by EY and the Manufacturing Institute found that the skills requirements for manufacturing roles are changing. As Industry 4.0 — that is, the Fourth Industrial Revolution, characterized by technological advancements like Internet of Things and AI integration, robotics, and big data in manufacturing — ramps up, technical roles are growing. According to Deloitte and TMI, over the past five years, there has been a 75% increase in demand for simulation software skills, especially for tech-enabled production and testing. This is followed by enterprise information management and cloud computing. Additional emerging manufacturing roles — like those dealing with semiconductor processing and electromechanical assembly — are also increasing.
Soft skills associated with customer service and critical thinking are also growing in importance, especially for entry-level roles that require aptitude and not necessarily hard knowledge.
Being able to test for both soft skills and hard skills — especially in a field that values know-how over paper — is paramount to making sure you make the right hires.
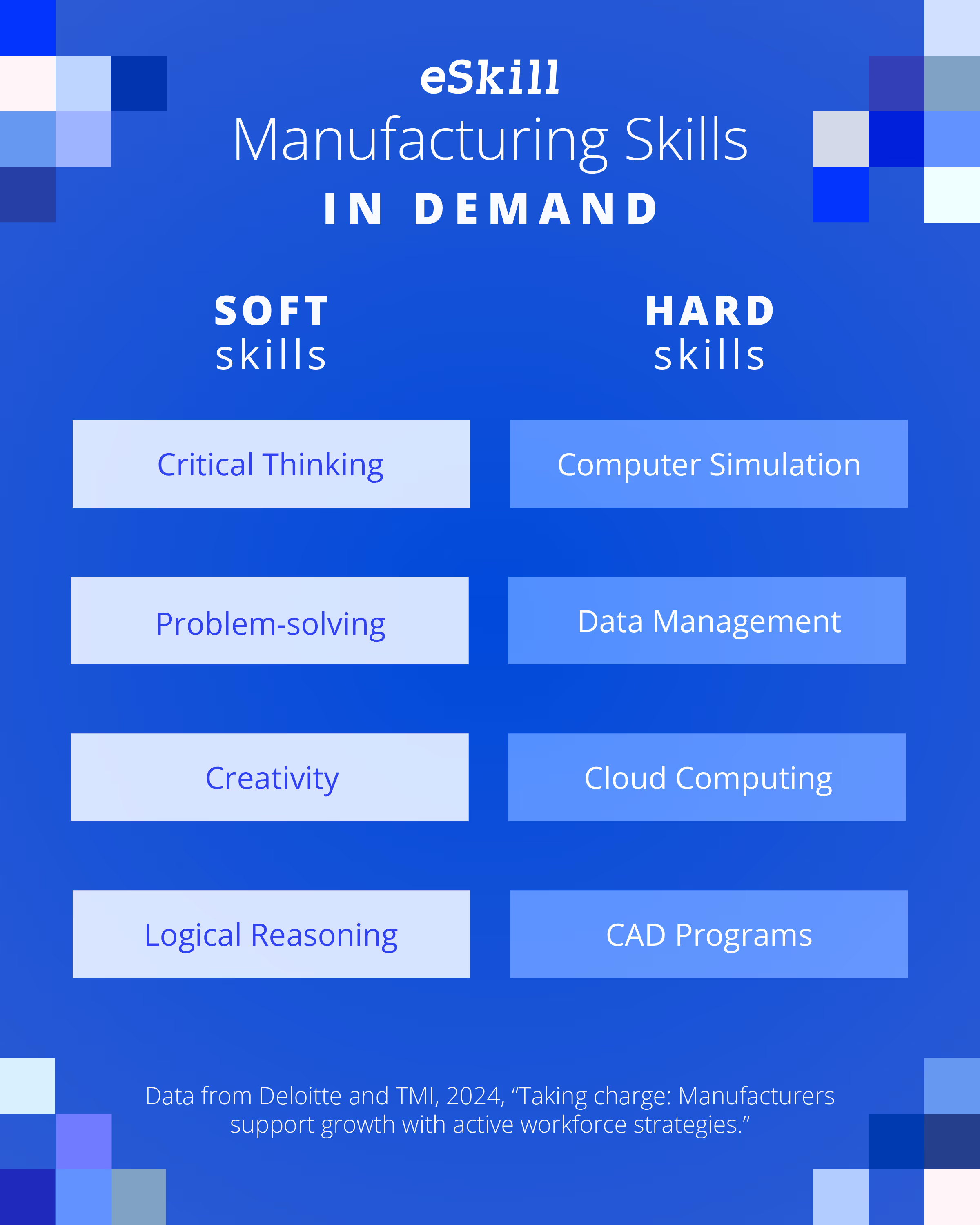
Gen Z misperceptions
Tech advancements, AI, data, and internet of things advancements are making the manufacturing industry more “intelligent” — as well as cleaner and safer. Factories aren’t the unsafe warehouses of yesteryear. They’re tidy and efficient. In fact, manufacturing is the leading sector in the US for innovation — accounting for 53% of private-sector research and development.
While the identity of the industry is changing, certain associations with manufacturing careers persist. While more Gen Zers are starting to consider careers in blue-collar fields, they’re not exactly chasing after manufacturing roles. Concerns over wages, safety, and flexibility are all pushing Gen Zers away from considering factory jobs.
How do you recruit and retain proficient workers?
How do you attract, and keep, the right talent? When nearly all manufacturers find hiring and retaining skilled labor a challenge to their business (especially due to competition from other sectors), it’s crucial to manufacturing as a whole to find, attract, and retain employees, especially with the threat of empty factories at hand.
How do you quickly find both entry-level and skilled workers who would do well on the job, and stick around?
Use pre-hire assessments
Pre-hire assessments can help you find those who have the aptitude (in entry-level roles) or the knowledge (in experienced roles) for the roles you need to fill before your competitors do. Additionally, you can test for soft skills to ensure candidates will thrive on their teams — improving job satisfaction and also reducing employee turnover.
Invest in the talent pipeline
Many manufacturing companies are pursuing partnerships with schools, community colleges, and certification programs to start individuals thinking about manufacturing careers early and build a talent pipeline — especially for roles involving robotics, automation, and data analysis. While the payoff for this investment will likely take years, it’s become an important initiative to closing the manufacturing gap, especially as more jobs in the industry continue to go unfilled.
Flexibility, meaning, and care
Gen Zers prefer flexibility in their work environment — like the ability to work from home — and place emphasis on work where they can find meaning. For younger generations, a sense of purpose has become increasingly important to their desire to stay in a job and their ability to thrive in it. Additionally, child care options are increasingly necessary for workers, especially following the pandemic.
Upskilling
Retaining workers means giving them opportunities for advancements, learning on-the-job, and progressing in their career. In fact, many employees are eager to upskill and take on new roles within their company.
Skills testing can help detect a baseline for where workers are at and where they lack. It can also serve to determine when they’re ready to move on to a new role in the company.
Minding the gap
The manufacturing skills gap is a worldwide crisis. The skills gap is deep, and it’ll take years, if not decades, for the talent pipeline to catch up, even as companies invest in early education programs and apprenticeship initiatives. While we wait for the industry to fill the gap, you can stay ahead of competitors by finding the right talent now.
Let’s face it — there is a limited talented pool in manufacturing at the moment. However, you can use a pre-hire assessment platform (like eSkill!) to find the talent and hire them before your competitors do. Evaluate technical proficiency, cognitive skills, and problem-solving abilities — as well as assess for interests and learning preferences — to determine both the aptitude of entry-level workers who would thrive in a role, and find certified high-skilled workers who have the know-how to work the software and equipment necessary to your own unique needs as a company.
No single company can close the manufacturing gap — but they can bridge it.
- How do you bridge the gap between a growing need for manufacturing hires and a shrinking number of qualified candidates — so you can stay ahead of competitors?
- What you need to know:
- Why is there a growing skills gap?
- Baby boomers exiting the workforce
- Decline in manufacturing education
- Changing skill requirements
- Gen Z misperceptions
- How do you recruit and retain proficient workers?
- Use pre-hire assessments
- Invest in the talent pipeline
- Flexibility, meaning, and care
- Upskilling
- Minding the gap
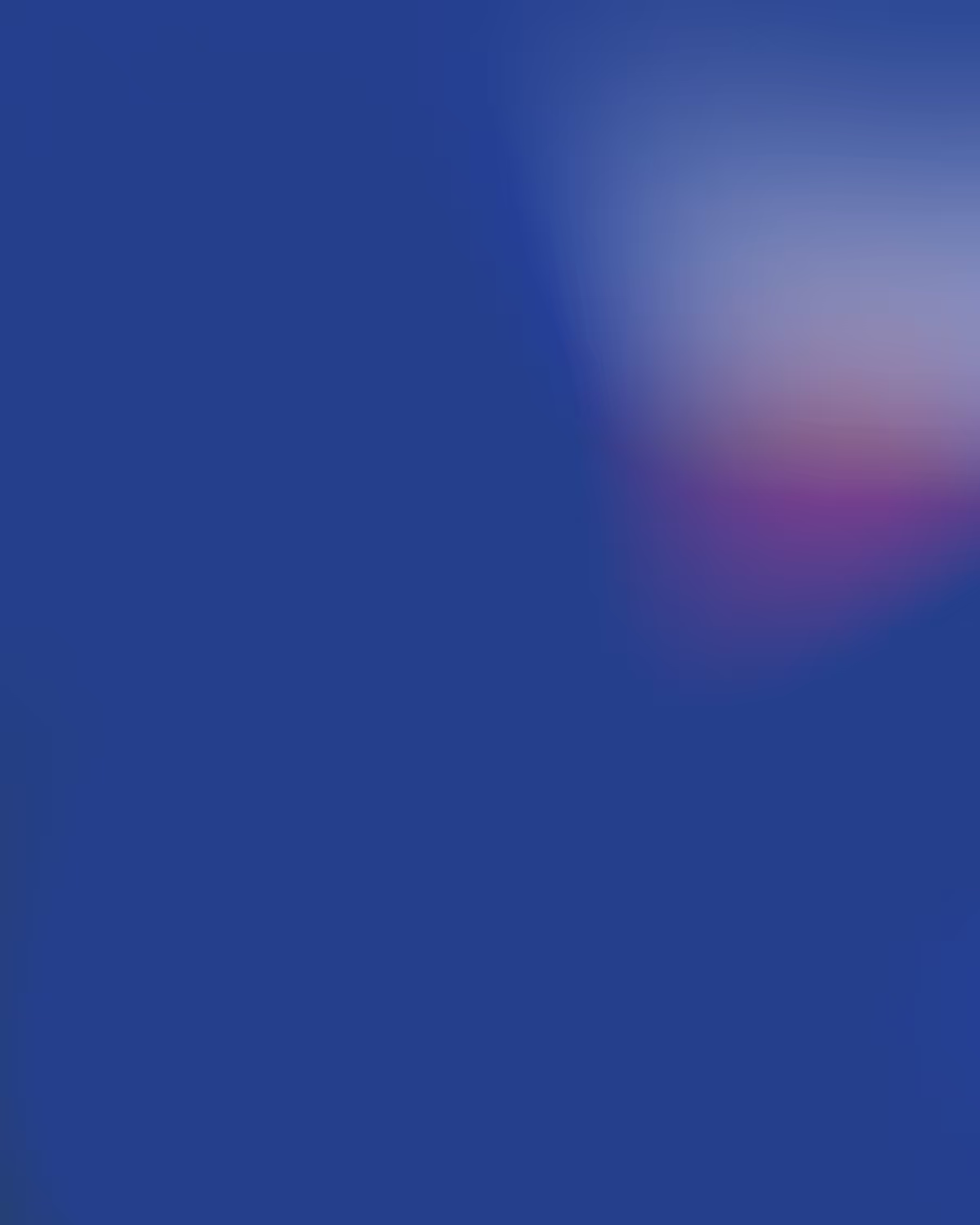
Sign up for our newsletter
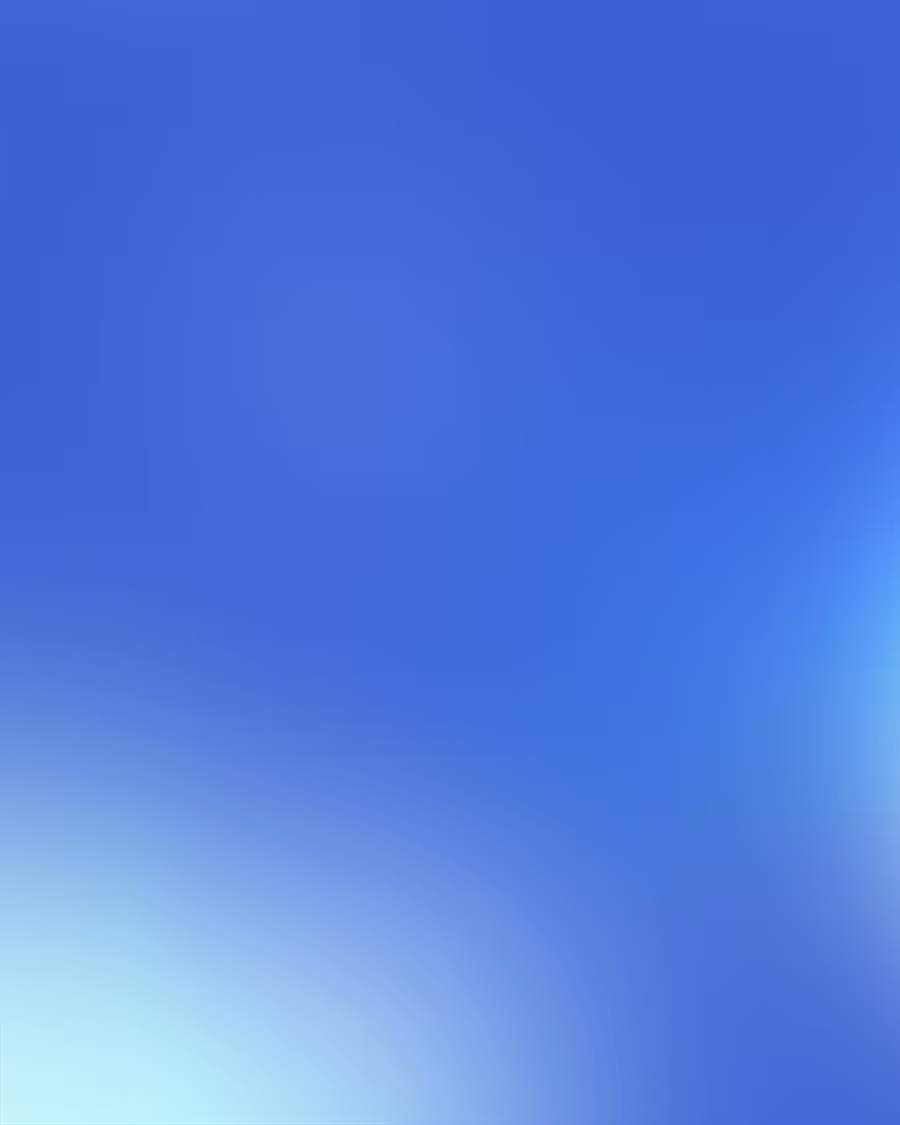
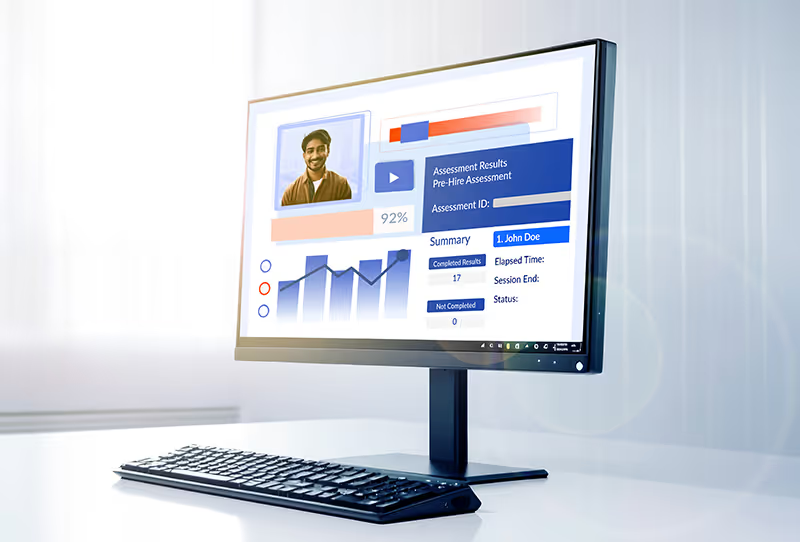